Why is Polyethylene Used?
Electro fusion has become the preferred method of joining polyethylene (PE) pipes. For insertion work and large diameter pipes (250 mm and beyond), the pipes must continue to be jointed by butt fusion.
The dynamics from traditional materials such as iron or steel to plastic for gas distribution piping systems was originally made because of the following advantages;
- Corrosion resistance both internally and externally.
- It provides good strength to weight ratio and ductile in fracture
- It is easily formed into complex shapes by extrusion, injection moulding etc.
- Reduction of transportation, material, and handling costs
- Easily joined
- It also provides the flexibility of buried system
- The pipe system is only as good as its joints
- Good working temperature (-20 to +50ºC)
- It is also resistance to chemical
- Ease of construction with semi-skilled labour.
Chemical Structure of PE Pipes
Polyethylene pipes used in the gas industry is very stable chemically and the higher quality types offer a very long service life. To appreciate the stability and long life offered by this pipe, it is necessary to examine the microstructure of the material.
Consider first the strength, hardness, chemical and heat resistance. Methane CH4, for example, which is the prime constituent of natural gas consists of one carbon and four hydrogen atoms as shown in figure. It has a chemical weight of 16 and is the only lighter than air hydrocarbon.
Methane Light Gas at STP
By adding a few carbon atoms and the appropriate number of hydrogen atoms we arrive at propane C3H8, which is known to be a heavy gas as shown in the figure below:
Propane Heavy Gas at STP
Adding yet more carbon and hydrogen atoms we can describe the structure of Hexane C6H14, which is a liquid at STP as you can see in the figure below:
Hexane Liquid at STP
Installation Procedure of the PE Pipelay
Electro-fusion Coupler
The Electro fusion process involves a Coupler and a Control box that allows the fusion joining of heat fusible materials to be implemented without the use of conventional hot iron fusion equipment.
The sizes of the electro fusion Coupler range from 63, 90, 125 and 180 mm diameter. The Coupler is designed to provide clearance between the pipe outside diameter and the Coupler inside diameter in all tolerance situations. The bore in the Unit is generally 1.1% > the nominal pipe OD, and thus enables easier assembly on new pipes. It’s also caters for creep in existing pressurised pipelines which may reqiure repairs or extension in the future.
Joint Assembled Prior Fusion
The heating coils are mono-filar in construction with a continuous coil wound from one socket to another, thus allowing fusion of both sides of a coupler in one operation. The coil terminations are electrically shrouded.
A visual indication that the fitting has been heated is contained in the outside surface of the fitting. The indicators operate on melt movement caused by a local relief of the fusion pressure.
A common fitting voltage is used throughout the system. The applied voltage is standardised at 39.5 volts (±0.5 volts) which keeps the current down to realistic levels (maximum 50 amps) whilst remaining below the recommended site safety level of 55 volts to earth. This standardisation on a single voltage pave the way for a simple universal control box capable of joining any manufacturers system, and the possibility of automatic fitting recognition.
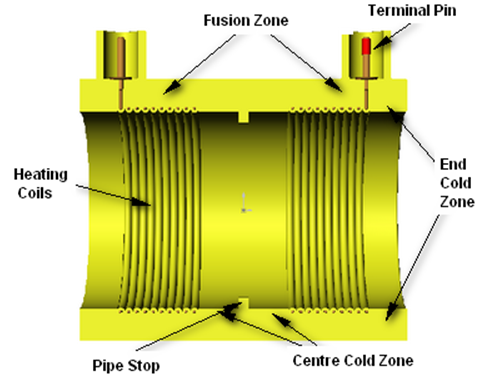
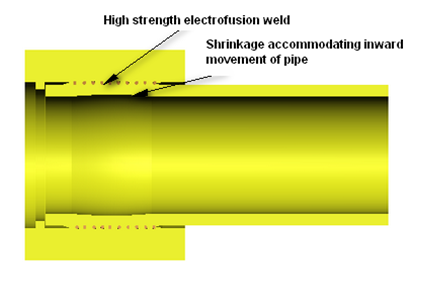
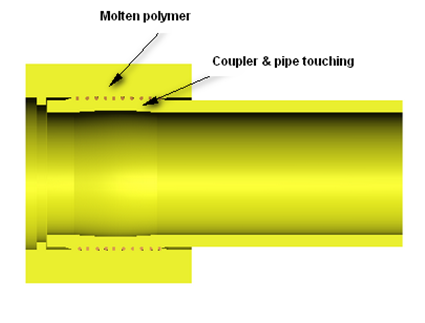